.jpg?filter=sharpen%28%29)
Kontaktperson
Stenersgata 1, bedre kjent som kontordelen av Oslo City. Et av Oslos høyeste bygg, midt i et av Norges travleste lyskryss. Kanskje mest kjent som oppholdssted for de handlelystne, og et mareritt for enhver entreprenør som er opptatt av god logistikk. Her tar aldri biltrafikken pause, det myldrer av mennesker og det foreligger strenge regler for anleggstrafikk.
Ventilasjonsanlegget i de fem øverste etasjene skal oppgraderes. Entra er byggherre og prosjektet er delt i to byggetrinn. Første trinn hadde oppstart høsten 2021 og ferdigstillelse er planlagt høsten 2023.
Da GK vant anbudet ble det raskt slått fast at dette prosjektet kunne egne seg som forsøkskanin i arbeidet for en grønnere byggeplass.
– Her var viljen til å tenke nytt på plass fra første dag så vi startet en prosess sammen med Lindab hvor målet var å redusere antall kjøreturer fra fabrikk til byggeplass, forklarer leder av utviklingsprosjektet og fagdirektør i GK, Mads Mysen.
Byggenæringen står for om lag 40 prosent av klimagassutslippene i verden. GK og Lindab er begge sitt ansvar bevisst, og opptatt av å ta grep for å bidra til mer bærekraftige byggeplasser.
– Nettopp fordi vi vil bidra til å redusere bransjens CO2-avtrykk har vi lenge ønsket oss en annen måte å frakte ventilasjonskanaler på. Så da dette prosjektet dukket opp fant vi ut at det var på tide å prøve noe nytt, forteller Ståle Svensson, salgssjef kanalsystemer i Lindab.
Se også:
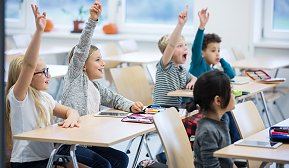
Ventilasjon
Les merTo tette og en badehette
Vanligvis innebærer frakt av ventilasjonskanaler at tre meter lange spirorør pakkes en og en ved siden av hverandre inn i lastebil. Denne praksisen skyldes i stor grad at ventilasjonsrør skal forsegles med plastlokk i hver ende for å oppfylle de strenge renhetskravene i prosjektene.
Men det måtte da være mulig å finne en annen måte å pakke kanalene på uten at det skulle gå på bekostning av kvaliteten på leveransen?
– Ved å pakke kanalene i hverandre, altså starte med den største dimensjonen og så tre neste dimensjon inn i hulrommet, og enda en dimensjon inn i der igjen, ble det mulig å frakte veldig mange flere meter med ventilasjonsrør per lastebillass, forteller Svensson.
Renhetskravet ble løst ved å plugge bunnen på den ytterste rørdimensjonen og så tre en plastpresenning, en såkalt badehette, over hele forsendelsen.
Enklere logistikk på byggeplass
Prosjektleder i GK, Knut Hauger, var raskt på ballen for å se hvordan denne måten å levere ventilasjon på kunne gi flere positive ringvirkninger.
– For min del handlet det mye om å løse den praktiske logistikken. Stenersgata 1 – kontordelen av Oslo City, er kjent for å være et vanskelig område å jobbe i. Og her skulle vi altså ikke bare frakte rørene fra fabrikken på Kalbakken og til sentrum, men også losse av midt i trafikken. Tilgangen til selve byggeplassen som ligger fem til ti etasjer over bakkenivå var også en nøtt å knekke.
– Vi kunne naturlig nok ikke frakte materialene inn gjennom kjøpesenteret, så alle kanalene måtte flyttes via en utvendig vareheis som vi raskt så var for smal til å romme metervis med ventilasjonskanaler.
Hauger tok nøyaktige mål av heisen, og gikk tilbake til tegnebrettet. Løsningen lå i å kutte lengden på rørene, samt å utvikle en egen transporttralle, skreddersydd for vareheisens innvendige mål.
– Det var først da vi kuttet kanallengden ned til 2,40 meter og pakket kanal-i-kanal- enhetene direkte på trallene med badehetten trukket over, at vi fikk dreisen på logistikken. Når disse trallene nå ankommer byggeplassen bruker vi mye mindre tid på å tømme bilen enn vi gjorde tidligere. Vi triller trallene rett inn i heisen og opp i riktig etasje, hvor kanalene blir liggende. Det betyr også mye tid spart for montørene som slipper å bære metervis med rør rundt på byggeplass, men nå ganske enkelt kan trille de med seg dit de skal.
Når trallene er tømt sendes de i retur til Lindab, som gjenbruker både disse og badehettene ved neste forsendelse.
Lønnsom bærekraft
– Denne måten å gjøre det på er ikke revolusjonerende i seg selv. Både det å frakte kanal i kanal og bruke traller har vært gjort før. Men dette er så vidt vi vet første gang det er satt i system og skreddersydd for et prosjekt, forteller Mysen.
Og effekten er merkbar.
– Frakter vi tre dimensjoner inne i hverandre dobles kanalvekten per bil. På turer der fem dimensjoner er pakket i hverandre er vi oppe i tredobbel vekt. I praksis betyr det at vi på dette prosjektet mer enn halverer antall turer til og fra fabrikk.
Videre reduseres plastavfallet med 157 kg per tur.
– Tiden brukt på å losse av, bære inn i heis og videre inn i etasjene er redusert med hele tre timer per leveranse. Når vi da tenker på at dette prosjektet skal løpe i to byggetrinn frem til ferdigstillelse i 2023, og at vi får to leveranser per uke blir det veldig mange arbeidstimer spart. Jeg tror alle kan være enige om at det er mye bedre å bruke arbeidstimene vi har til rådighet på å montere enn å sjaue, oppsummerer prosjektleder Hauge.
Også montørene gir uttrykk for å være fornøyd med den nye logistikkløsningen.
– I tillegg til at det blir mindre fysisk slitasje ser vi at risikoen for skader reduseres.
For Lindab betyr naturlig nok denne måten å pakke kanalene på noe merarbeid på fabrikken.
– Men dette sparer vi inn ved å bruke færre timer på veien. I det store bildet handler dette om å være villig til å gjøre de endringene vi faktisk kan innenfor regelverket. Og vi er nødt til å være tilpasningsdyktige. Vi kan ikke fortsette å frakte luft i store kvanta og samtidig snakke om bærekraft, slår Svensson fast.
Se også:
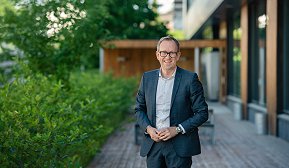
GKs års- og bærekraftsrapport 2021: Vi rigger for lønnsom og bærekraftig vekst
Les merVi må tørre å tenke nytt
– Dette prosjektet har vist oss at det å prioritere bærekraft hverken trenger å være noe dyrere eller vanskeligere enn å fortsette som før. Det er ikke alltid nødvendig å tenke så stort eller gjøre seg avhengig av støtteordninger som ofte fører med seg mye byråkrati. Vi kommer langt med å ha et felles ønske om å få til noe og ikke minst sette oss ned og diskutere oss frem til løsninger som vil fungere i praksis, konkluderer Mysen.
Også Knut Hauger roser det gode samarbeidet i prosjektet.
– Da vi presenterte løsningen vår for Entra ga de raskt uttrykk for at dette var noe som kunne være positivt for alle parter. Vi opplevde at de satte pris på at vi forsøkte å tenke utenfor boksen.
Både GK og Lindab håper denne måten å transportere ventilasjonskanaler på etterhvert vil bli en bransjestandard. Og ikke bare i prosjekter med trøblete adkomst. Så lenge kravene til renhetsklasse kan oppfylles ser Mads Mysen stort potensiale også utenfor urbane strøk.
– Når vi ser hvilken effekt dette har hatt i et område som ligger såpass nært fabrikken, tenk bare på hvor mye CO2 vi kan spare på prosjekter hvor kanalene skal fraktes over lange avstander.
En felles innstilling om at dette er løsbart har vært, og vil fortsatt være avgjørende for økt bærekraft i bransjen.
– For å lykkes med arbeidet for en grønnere byggenæringen er vi helt avhengig av at noen tør å ta initiativ til å tenke nytt, og så må noen være villig til å teste ut de tankene i praksis, avslutter Ståle Svensson.